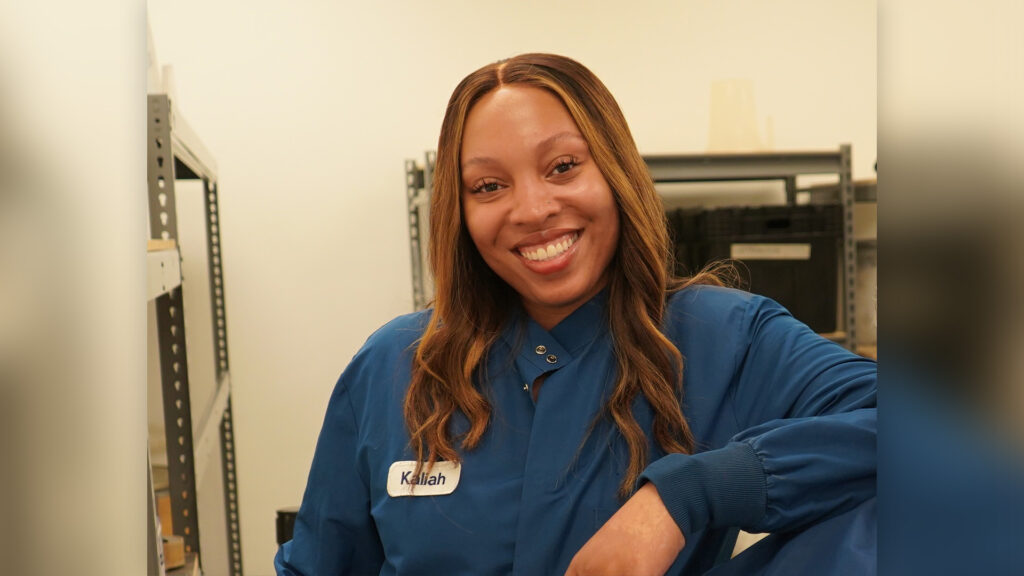
Taking Paint to New Heights: HII Senior Chemist Combines Scientific Passion with Space Innovation
When Kaliah Jackson, a senior chemist and program manager at HII’s Advanced Materials Coatings Lab in Illinois, graduated from South Carolina State University with a bachelor’s degree in chemistry, she never imagined her career would take her to new heights — impacting space exploration.